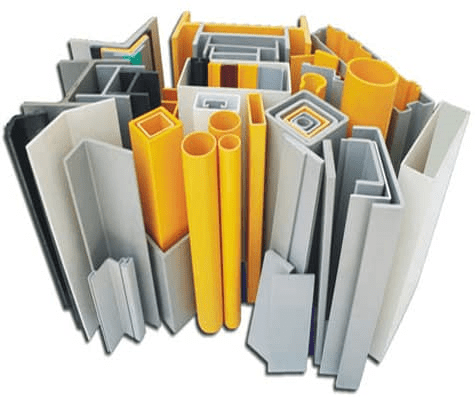
Pultruded profiles products are becoming a success in the global manufacturing economy, thanks to FRP pultruded profiles manufacturers. Pultrusion is among the preferred type of composite parts for thousands of products in important markets like telecom and infrastructure.?
Pultruded products are predicted to be among the most promising segments of the composites market over the next decade. The global pultrusion industry is expected to grow with an estimated amount of $3.0 billion by 2023. The forecast growth is at a CAGR of 4.1% from 2018 to 2023 as per market research from Lucintel.
Pultrusion Process ? What is it?
Pultrusion is a manufacturing procedure that converts liquid resin and reinforced fibers into a fiber-reinforced plastic through a pulling method, instead of extrusion. The resulting plastic composite is known as a Fiber-Reinforced Polymer (FRP).
There are two essential kinds of pultrusion systems. One is continuous (cat track), and the other is reciprocating (hand over hand).
- Rovings (narrow bundles) of fiber reinforcements (normally carbon or glass) are positioned tactfully by creels for right placement in the composite before you feed into a guide plate.
- The principal pultrusion step is to get the fibers ceaselessly through resin impregnator to be soaked. The resin shower or wet-out may incorporate epoxy, polyurethane, polyester, or vinyl ester.
Fillers and different added substances, for example, colorant, fire inhibitors, and UV retardants, are regularly mixed into the procedure to expand the appeal, destructive obstruction, and long haul execution of the completed item.
As the soaked fibers leave the impregnator, they enter the “pre previous” device, which presses out excess resin and assists with forming the fiber reinforcements.
This resin-impregnated, fiber strengthened composite is then gotten through a reliably warmed steel pass on to fix the thermosetting resin and make a solidified polymer of the desired shape.
The hardened FRP is additionally pulled towards the blade and where it can be cut to the desired length. Personalized urethane pull blocks stop the finished profiles from being distorted, cracked, or deformed during this final step of pultrusion. This final product produced by FRP pultruded profiles manufacturers is lightweight and strong.
Common Applications of Pultruded Profiles and Products
A few of the most common uses for pultruded products include items created to support:
Utilities – for products such as cross arms, utility poles, and
- Line markers; electrical lines and trunking;
- Wastewater and water treatment components;
- Non-conductive ladder rails; and
- Fiber optic cabling.
Infrastructure – for products like:
- Corrosion-resistant guardrails;
- Bridge components;
- Railway crossing arms;
- Antenna housing; and
- Highway sound barriers.
Construction – for items such as commercial and residential window, frame and door, profiles and reinforcements; electrical and pipe supports; and roll-up door panels.
Other applications for pultruded products include a plethora of verticals, and include:
- Cored tubing
- Struts
- Perimeter fencing
- Tool handles
- Static arrestors
- Cable trays
- Demisting blades
- Armor plate
- Refrigeration components
- Seating
- Hand and guard rails
- Decks
Industries that rely vigorously upon pultrusion for specific manufactured parts that are solid and lightweight incorporate the engine vehicle. Further railroad and aviation manufacturing verticals, such as development, electrical, mechanical, compound, and structural designer segments, also depend on pultrusion.
Pultrusion allows cost-effective, rapid, high-volume non-stop manufacture of structural profiles that are durable, strong, lasting, and lightweight.
Pultruded profiles products are inexpensive and easy to transport, encourage future thinking for simplified manufacturing of consumer or industry facing solutions, and perfectly mesh with global sustainability objectives.
Infrastructure Forecasted to be Big Growth Driver for Pultrusion Industry
The infrastructure market is predicted to be one principal growth driver for pultruded composites. Pultruded profiles serve as a probable replacement for conventional steel rebar in the face of rising tariffs and shrinking supply.
Steel rebar consumption is liable for monstrous asset management costs that need huge investment for a structure’s lifespan to cure issues with a strengthened solid framework. In the US, more than 54,000 out of 615,000 scaffolds are considered structurally lacking.
Steel rebar is a $200 million worldwide market. Detailed examination has demonstrated that glass fiber strengthened plastic (GRP) rebar can possibly keep up its microstructural honesty and mechanical properties for longer than 15 years. This can give significant upgrades in strength, decreases in life cycle cost decrease, and improved long haul execution for infrastructure proprietors.
The Halls River Bridge in Florida is a cutting-edge bride, which was specifically propelled to exhibit the unwavering quality and advantages of composite materials. The materials include pultruded FRP rebar used in different points in the superstructure, including the barriers, deck, approach slabs, and components of the base and sheet heap walls.
Further Growth Opportunities for implementation of pultruded products
There are several other industries, sectors, and verticals able to receive massive benefits from pultrusion methods and pultruded profiles.
For 5G building and infrastructure elements – Pultruded fiberglass laminates can offer durability and installation benefits while minimizing attenuation of the shorter wavelength 5G signals.
Spar cap structures for more slender and longer wind turbine blades can be refined with pultruded composites to enhance turbine efficiency.
In the oil & gas industry – corrosion-prone steel sucker rods can be supplanted with lightweight pultruded carbon fiber composites. This will help for lower installation, energy, and maintenance costs.
Normalization activities in the US and Europe will have a huge influence on figuring out who rapidly and proficiently adopt pultruded composites across developing markets.
Innovations – that can aid non-ruinous testing, just as new advances in resin frameworks. Curing specialists can securely speed up without trading off the final product, will likewise have an influence as pultrusion items acquire the piece of the overall industry over all verticals.
The market demand for pultruded profiles and products is forecasted to be a dominating factor over the next five years. Structural composites with high strength are vital for the success and cost-effectiveness of the following:
- Cooling towers,
- Offshore oil drilling projects, and
- Civil engineering projects.
All of the above will trigger demand for pultruded composites.
Pultruded products provide high-level heat and corrosion resistance, massive strength-to-weight features, dielectric attributes, and dimensional stability. All of these can provide benefits to designers on construction projects. Also, pultruded composites weigh almost 75% less compared to steel counterparts. As a result, transportation becomes a significant factor in its popularity.
Pultruded Products? Sustainability
One of the major attributes of pultruded products (excluding cost-efficiency of transportation, manufacturing, and reduced asset management) is their sustainability. Pultruded composites are durable, have a stretched service life, and low maintenance needs. This results in a lower consumption of energy throughout the product’s life; at that point, many can be recycled.
The capacity of pultrusion composites to supplant steel and aluminum is more essential than any other recently, even with tariffs and transportation costs. While aluminum expulsion items represent roughly 15% of the entirety of the aluminum devoured, composite pultrusion items represent just 5% of every single strengthened plastic created. This leaves space for mind-blowing market development for pultruded items, which can build manageability on a global level.
Additional Advantages of Pultruded Composites
The process of pultrusion manufacturing can manufacture almost any consistent cross-sectional shape in nearly any size. The flexibility allows penetration of a wide range of market areas. Specific markets attract benefits from pultruded products beyond price competitiveness. The advantages are all due to FRP pultruded profiles manufacturers, which conventional competitive materials cannot supply.
Electromagnetic transparency:
Telecoms and remote organizations can profit by fiberglass pultrusion’s capacity to be promptly infiltrated by radio waves for the help of two-way radios, phones, WiFi, or Bluetooth associations.
Electrical insulation:
Safety is expanded in enhanced situations of nonconductive pultruded fiberglass dealt with instruments and fiberglass pultrusion stepping stools giving protection from electrical shock.
Abrasion resistance:
Construction verticals can take advantage of fiberglass pultruded products. Pultruded profiles resist both alkaline and acidic corrosives, making them perfect for use in outdoor or extreme environments.
Heat insulation:
The reduced thermal transmittance offered by fiberglass pultrusion minimizes condensation and support installations that need the retention of thermal characteristics via a wall cavity or on the surface.
Conclusion
For any undertaking requiring predominant dimensional stability, simple transportation and establishment, close resistance to specified boundaries, and low support over quite a while period, pultruded composite items provide. It’s the manageable, practical arrangement not of the future but of the present time and place.

As the editor of the blog, She curate insightful content that sparks curiosity and fosters learning. With a passion for storytelling and a keen eye for detail, she strive to bring diverse perspectives and engaging narratives to readers, ensuring every piece informs, inspires, and enriches.