As printed circuit boards become denser and more complex, the potential for repairs and rework increases significantly. Even if technicians use the most advanced component placement layouts, it?s impossible to rule out the risk of assembly defects. When these defects happen, PCB manufacturers will either have to perform the rework independently or employ third-party PCB rework specialists. Either way ? the demand for skilled PCB rework specialists is very high across the global electronics manufacturing industry.
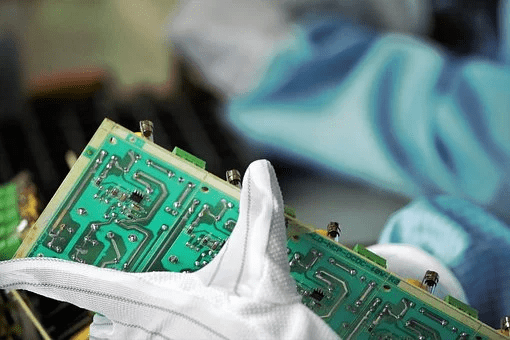
When electronics assembly technicians enrol in PCB rework training, they?re not just better equipped to handle rework requirements. They?re also educated enough to plan ahead in their designs and minimize the risk of assembly defects. For instance, some sensitive circuits need more testing than others. A technician with expertise in PCB rework processes will be able to address the risks involved with using such sensitive circuits preemptively. Then, they can conduct planned testing during the PCBs? developmental stages and minimize the risk of circuit defects.
An assembly technician with expertise in PCB rework can –
- Identify areas of a PCB that?ll require more testing or more room for potential rework in the future.
- These highly skilled manufacturing technicians also possess the engineering skills to conduct the PCB rework process.
Hence, training for PCB rework processes significantly boosts the capabilities of electronics assembly technicians, soldering professionals, and pretty much anyone involved in the manufacture of electrical components.
What Does PCB Rework Entail?
To understand what an expert of PCB rework does, we must understand the major reasons why rework requirements pop up in the first place. In every PCB manufacturing project, some degree of rework is always expected. Suppose the technicians handling the project are experts in PCB rework. In that case, they?ll be able to avoid excessive amounts of potential rework requirements by following all IPC guidelines regarding the assembly of complex PCBs. However, many potential defects and rework requirements are almost unavoidable. They inevitably lead to rework requirements –
- Wrong Parts ? Sometimes, a wrong part gets specified to the technicians. Later, the manufacturers alter their demands, and the whole batch needs to be either disposed of or reworked.
- Assembly Defects ? Assembly defects like improper soldering or insufficient cleaning can lead to expensive rework requirements.
- Complications ? Since modern-day PCBs are so small, many of the components on the boards are hidden by other parts, or it?s impossible to touch some components because they?re so tightly positioned. In many cases, closely located components get soldered together due to excessive exposure to heat. These complications inevitably lead to rework requirements.
It?s almost impossible for manufacturers to avoid rework. Such is the intricate nature of modern PCBs. That?s why, to get their circuit boards built-in time and cost-effective manners, these companies prefer hiring professionals who know all about PCB rework. After all, rework is still less expensive than restarting the manufacturing process or getting rid of all the ?defective? boards altogether.
The Tools of Rework Specialists
Contrary to belief, PCB rework isn?t a highly labor-intensive process anymore. Top PCB rework specialists use tools that help them speed up repair operations such as –
- Ergonomic Workstations: Since PCB rework experts need to be highly dexterous and concentrated while performing repairs, they need ESD-grounded workstations (Electro-Static Discharge) with high-quality lighting to improve the efficiencies of their efforts.
- Stereo Microscope: Precision repair and rework are impossible without microscopes. 100% of rework operations that have been conducted without microscopes have failed. The clarity offered by high-quality optics cannot be matched even by advanced video recording devices.
- Latest Soldering Tools: Traditional soldering tools aren?t good or precise enough to facilitate rework on super-dense PCBs. Hence, PCB rework specialists need to use ergonomically designed soldering tools that come with wide ranges of small tips.
- Component Displacement Tools: For efficient component removal via techniques like infrared heating or contact heating, PCB reworks specialists need the latest component displacement tools.
Other tools required for PCB rework processes include preheating stations, SMT component removal tools, infrared heaters, micro-grinding tools, and precision drilling systems. What?s even more important for PCB rework specialists is abiding by industry standards while executing repair and rework projects.
The IPC Standards for PCB Rework
All technicians interested in learning about PCB rework and repair need to follow the IPC 7711/21 standard. To do so, they must achieve IPC 7711/21 certification. This rework certification training is the fundamental ?How To?? guide on PCB rework processes. If technicians want to know how the global electronics industry wants them to remove and replace components on PCBs, they need to master the IPC 7711/21 standard.
This certification is designed to assure valid, reliable, and accurate assessments of PCB rework requirements. Any professional with this certification will receive professional recognition for their rework skills across the world. More importantly, the educational-based training they receive puts them in a better position to learn about evolving technologies in PCB rework processes.

As the editor of the blog, She curate insightful content that sparks curiosity and fosters learning. With a passion for storytelling and a keen eye for detail, she strive to bring diverse perspectives and engaging narratives to readers, ensuring every piece informs, inspires, and enriches.